In February of this year, the Ministry of Industry and Information Technology's website released the operational status of China's lithium-ion battery industry in 2022. The national production of lithium-ion batteries reached 750 GWh, an increase of over 130% compared to the previous year. Among them, the production of energy storage lithium batteries exceeded 100 GWh. The first-tier materials in lithium batteries, including cathode materials, anode materials, separators, and electrolytes, had production volumes of approximately 1.85 million tons, 1.4 million tons, 13 billion square meters, and 850,000 tons, respectively, all experiencing growth rates of over 60% compared to the previous year. The industry scale further expanded, with the total output value surpassing 1.2 trillion yuan.
In the future, as electric vehicles, as a low-carbon force, continue to penetrate the market, and with the continuous decline in the cost of energy storage lithium batteries, the proportion of lithium batteries applied in the energy storage field will increase. The lithium battery industry has broad development prospects, which will promote the continuous growth of the electrolyte market.
The electrolyte is mainly composed of three parts: lithium salts, organic solvents, and additives. The cost of the electrolyte is relatively small but determines the comprehensive performance of lithium-ion batteries. Currently, 95% of the electrolyte solvents are carbonate esters, including dimethyl carbonate (DMC), diethyl carbonate (DEC), ethyl methyl carbonate (EMC), ethylene carbonate (EC), and propylene carbonate (PC). Linear carbonate esters account for approximately 60% of the solvent mass, mainly divided into dimethyl carbonate (DMC), diethyl carbonate (DEC), and ethyl methyl carbonate (EMC). The proportions of these solvents vary significantly in different types of batteries. Generally, EMC has a higher proportion in ternary batteries, while DMC has a higher proportion in lithium iron phosphate batteries.
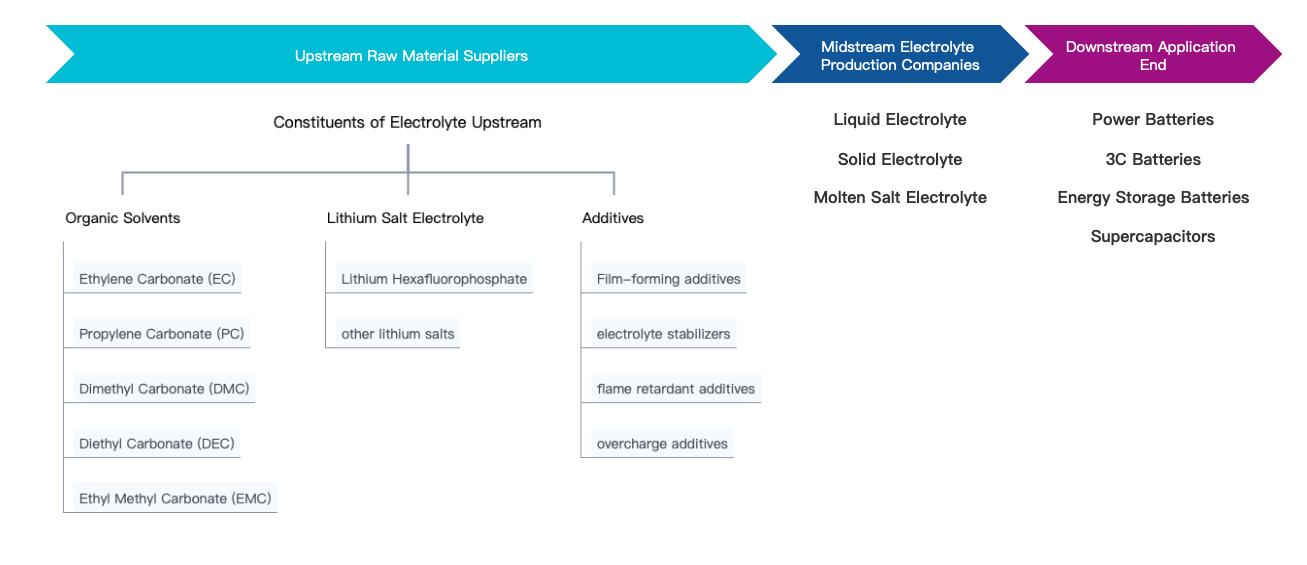
Electronic grade carbonate industry chain and process route
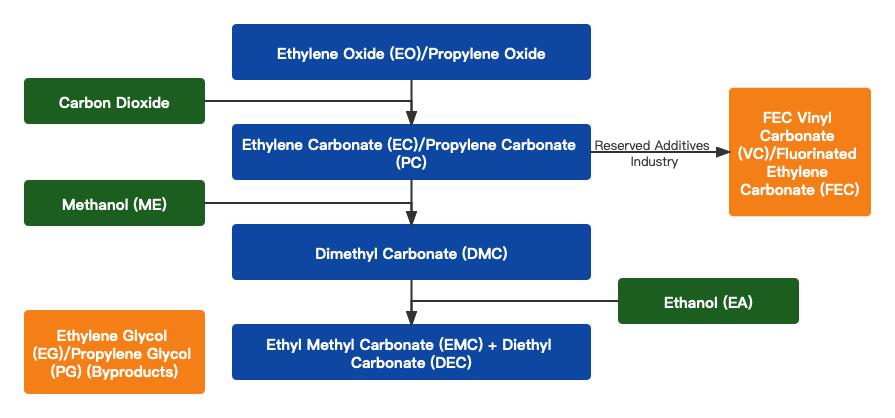
Carbonate Ethyl/Propyl Acrylate Process Route
The epoxy ethyl/propyl and carbon dioxide addition method - this reaction process involves the use of carbon dioxide.
With the implementation of the "CCUS" strategy in recent years, utilizing recycled CO2 to produce carbonates has become a new development approach, especially in the application of lithium-ion batteries.
The reaction for the preparation of carbonate ethyl/propyl acrylate through the addition reaction of epoxy ethyl/propyl and carbon dioxide is exothermic and results in volume reduction. From a chemical equilibrium perspective, low temperature and high pressure conditions are favorable for the progress of the reaction. The selection of an appropriate catalyst is crucial for the successful implementation of the reaction.
The system for this reaction mainly consists of homogeneous catalytic systems and heterogeneous catalytic systems. Currently, in domestic carbonate ethyl/propyl acrylate production methods, three generations of catalytic technologies have been developed. However, without exception, they all use homogeneous catalysts, which have a low technical threshold. Most domestic manufacturers use first-generation catalysts, while a few domestic and foreign manufacturers primarily use second- and third-generation catalysts. The quality of domestic products in terms of color and impurity content is significantly lower than that of products produced using second- and third-generation catalysts. The newly developed fourth-generation heterogeneous catalyst does not introduce catalyst components into the product during the reaction, eliminating the need for catalyst separation and simplifying the separation process between the homogeneous catalyst and the reaction product.
Furthermore, the fourth-generation catalyst is enhanced with nanomaterials, resulting in a thermal stability (decomposition temperature) increase of more than 15°C and a chemical swelling of less than 5% compared to commercial ion exchange resins. However, the evaluation of catalyst deactivation remains a challenge, and currently, only one manufacturer in China uses this catalyst, while the vast majority of manufacturers still opt for homogeneous catalysts.
Dimethyl Carbonate (DMC) Process Route
The ester exchange method is the mainstream process in the current DMC industry, with the combined capacity of ester exchange method synthesis devices accounting for more than 87% of the total DMC production capacity. This process has high production safety, high yield, and a high level of industrialization. Additionally, the co-production facility can produce at least four types of carbonate solvents, adding higher value. The ester exchange method is the mainstream process route in China and can be divided into two routes: the propylene oxide route and the ethylene oxide route.
Propylene Oxide Route:
This is a new process that combines propylene oxide (PO), carbon dioxide (CO2), and methanol (ME) to produce dimethyl carbonate (DMC) and propylene glycol (PG). The reaction is conducted in two steps: the reaction between CO2 and propylene oxide to form propylene carbonate, followed by the ester exchange reaction between propylene carbonate and methanol to produce dimethyl carbonate and propylene glycol.
The first step involves the reaction of propylene oxide and carbon dioxide under the catalytic effect, resulting in the formation of propylene carbonate. The reaction equation is as follows:
PO + CO2 → PC
The second step involves the reaction between propylene carbonate and methanol to produce dimethyl carbonate and propylene glycol. The reaction equation is as follows:
PC + ME → DMC + PG
This ethylene carbonate synthesis process is relatively mature in China and is currently the main production process route for battery-grade DMC.
Ethylene Oxide Route:
This is a new process developed by Texaco in the United States that combines ethylene oxide (EO), carbon dioxide (CO2), and methanol to produce dimethyl carbonate (DMC) and ethylene glycol (EG). The reaction is conducted in two steps: the reaction between CO2 and ethylene oxide to form ethylene carbonate, followed by the ester exchange reaction between ethylene carbonate and methanol to produce dimethyl carbonate and ethylene glycol.
The ester exchange method for producing dimethyl carbonate has good economic and social benefits, as it operates under mild reaction conditions and requires relatively small equipment investment. Furthermore, the byproduct, ethylene glycol (EG), has better market stability compared to propylene glycol (PG) in the PO method.
The reaction equation for the EO ester exchange method for producing dimethyl carbonate is as follows:
(CH2)2O + CO2 → (CH2O)2CO
(CH2O)2CO + CH3OH → (CH3O)2CO + CH2OHCH2OH
This process can utilize heterogeneous supported catalysts, completely solving the challenge of separating homogeneous catalysts and methanol sodium in the ester exchange process.
Ethyl Methyl Carbonate (EMC) Process Route
Currently, the ester exchange process using DMC and ethanol is commonly adopted in China. The raw materials for DMC and ethanol ester exchange are readily available, and the byproduct methanol can be used as a raw material for DMC production. This process is particularly suitable for DMC manufacturers to produce EMC. The process has the advantages of low toxicity in raw materials and intermediate products, no "three wastes" generated during the reaction, small equipment investment, simple process, high product purity, shortened production process, extended product line, and reduced cost.
DMC and ethanol ester exchange reaction can be represented as follows:
CH3OCOOCH3 + C2H5OH → CH3OH + C2H5OCOOC2H5 + CH3OCOOC2H5
The DMC and ethanol ester exchange reaction to synthesize EMC is a reversible reaction, and its equilibrium constant is larger compared to the DMC and DEC ester exchange reaction to synthesize EMC. The reaction employs alkali metal carbonates or alkali metal organic salts as catalysts. When the amount of DMC is appropriate, EMC is mainly produced. When there is an excess of ethanol, ethanol will further react with EMC to produce DEC.
DODGEN Electrolyte Process Technology Advantages
Catalyst Upgrading: Homogeneous third-generation catalyst is used in the EC unit, while heterogeneous catalysts are used in the DMC/EMC unit.
Comprehensive Heat Utilization: Heat pump rectification technology saves steam; comprehensive utilization of low-temperature heat grading.
Product Quality Upgrading: EC/DMC/EMC/DEC are all upgraded to battery-grade product quality standards; ethylene glycol byproduct meets polyester-grade product quality standards.